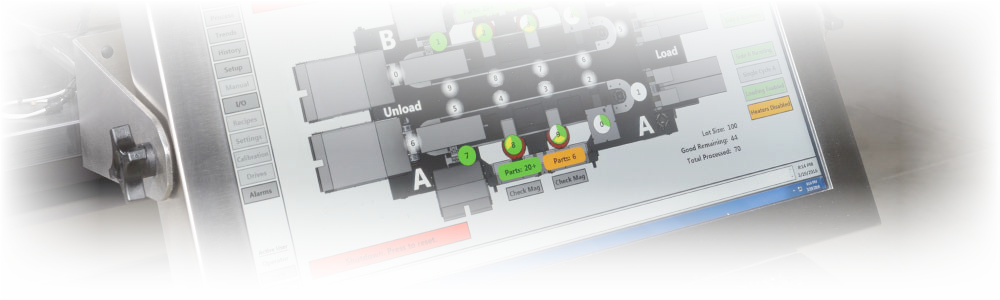
Software Solutions
Our software solutions are the backbone of the machines we build. We use a modular software structure and modern PLC schemas such as Sequential Function Chart and Function Block on a range of platforms.
Custom Software is the Key
Custom software makes granular control of each machine and process possible. Whether it’s tension control for web handling, servo-based force control, recipe handling, or complex parallel and asynchronous sequencing, the software is what makes it possible. In addition to reliable functionality, it’s important that the end-user gets the experience they’re looking for. That’s why we use a variety of HMI platforms like Inductive Automation, Maple Systems, Red Lion, Beijer, and others depending on the machine and customer preference. We also offer a custom-built HMI system constructed from the ground up using the Microsoft.NET Framework, which is lightweight, can run on any Windows PC with minimal installation, and is highly flexible with access to all Windows functionality.
Custom Software is the Key
Custom software makes granular control of each machine and process possible. Whether it’s tension control for web handling, servo-based force control, recipe handling, or complex parallel and asynchronous sequencing, the software is what makes it possible. In addition to reliable functionality, it’s important that the end-user gets the experience they’re looking for. That’s why we use a variety of HMI platforms like Inductive Automation, Maple Systems, Red Lion, Beijer, and others depending on the machine and customer preference. We also offer a custom-built HMI system constructed from the ground up using the Microsoft.NET Framework, which is lightweight, can run on any Windows PC with minimal installation, and is highly flexible with access to all Windows functionality.
Smart Manufacturing and OEE
You already know that data collection and reporting are essential to maximizing efficiency. You need to know everything happening on your production floor from lot and part handling to machine errors and downtime. More importantly, you need to be able to interpret and present that information in a meaningful way. That’s why we work closely with our customers to ensure that our machines integrate with your data collection system of choice. Alternatively, when using Ignition by Inductive Automation or our in-house HMI, the data collection can be built directly into the machine without having to rely on a third party.
SCADA and More
Ignition by Inductive Automation is Lehnen Industrial’s solution of choice for high-level systems. This powerful SCADA framework is capable of combining HMIs and data collection in one system. It is a centralized, scalable solution suitable for single machines or multi-machine networks. Ignition is flexible, customizable, and it handles complex functionality efficiently. It accommodates PC or web-based operator interfaces, and its simple, honest licensing system and sleek, modern aesthetic make it an easy choice. Ignition can be configured to integrate and monitor your entire industrial operation or to provide the missing communication link for other systems like Rockwell Historian, OSI Pi, AspenTech, Delta V, and more.
SCADA and More
Ignition by Inductive Automation is our solution of choice for high-level systems. This powerful SCADA framework is capable of combining HMIs and data collection in one system. It is a centralized, scalable solution suitable for single machines or multi-machine networks. Ignition is flexible, customizable, and it handles complex functionality efficiently. It accommodates PC or web-based operator interfaces, and its simple, honest licensing system and sleek, modern aesthetic, make it an easy choice. Ignition can be configured to integrate and monitor your entire industrial operation or to provide the missing communication link for other systems like Rockwell Historian, OSI Pi, AspenTech, Delta V, and more.
Tailored Software Solutions
That’s why we chose to use Ignition when we decided to develop a framework for collecting and aggregating OEE (Overall Equipment Effectiveness) data from diverse and dissimilar machines. Our custom, per machine, approach avoids the pitfalls of “one size fits all” solutions, which can struggle to integrate with existing equipment. Whether coming from new builds, older validated machines, or even entered by hand, this flexible system can bring data together into a common SQL database where it becomes accessible in real-time. From there, data can be browsed, analyzed, used to create reports directly from our Ignition-based dashboard, or accessed from another third-party system if desired. We work closely with our customers to make sure the design matches your needs. The system can be expanded to include lot, serial, and/or SPC (Statistical Process Control) data as well.
“They have a great understanding of the customer’s process and foresight to predict different scenarios and account for even minor operational errors up front. However, the software and data collection portion of our project was probably the most impressive.”
“I haven’t seen a single error in data being sent incorrectly to the database.”